Selection of Appropriate Paint Strippers
STRIP AWAY REMOVES COATS OF WILL NOT REMOVE SAFE ON SURFACES OF AVOID STRUCTURES MADE OF STRIP AWAY LV REMOVES COATS OF WILL NOT REMOVE SAFE ON SURFACES OF AVOID STRUCTURES MADE OF * Note: STRIP AWAY LV may be used on these surfaces providing dwell time is controlled and limited (test first)
Guide: Tiling On Floating Floors
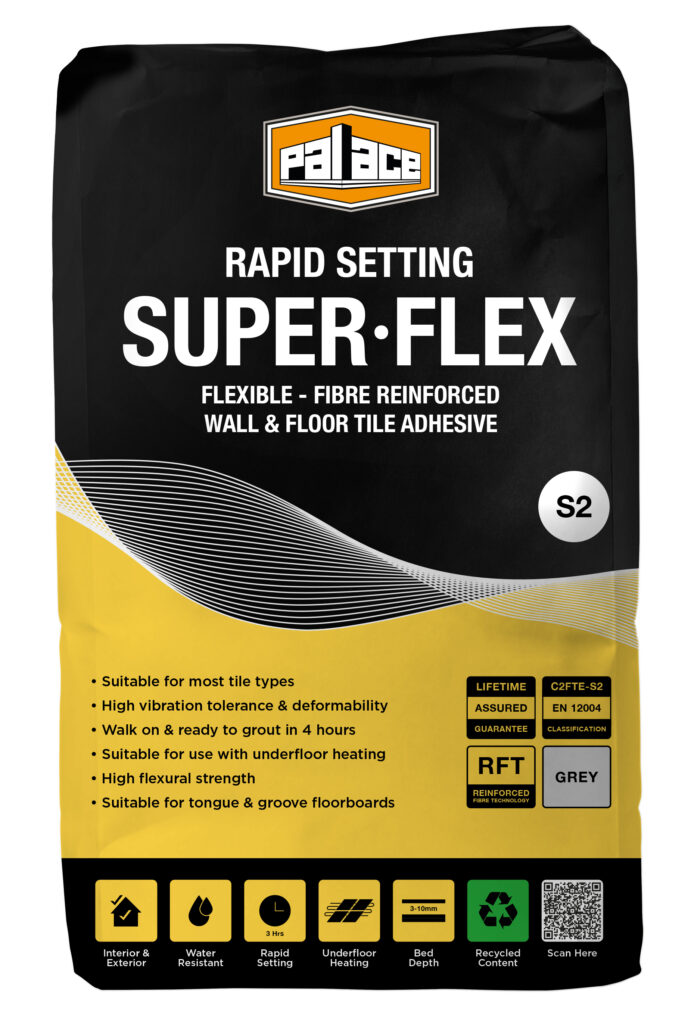
DESIGN CONSIDERATIONS All tile fixing should be carried out in accordance with BS 5385: WALL & FLOOR TILING Part 3 1989 – Code of practice for the design & installation of ceramic floor tiles and mosaics. Section 14.4 of this standard emphasises the need for timber substrates to be more than suitable for carrying the […]
Guide: How to Grout & Avoid Colour Variations
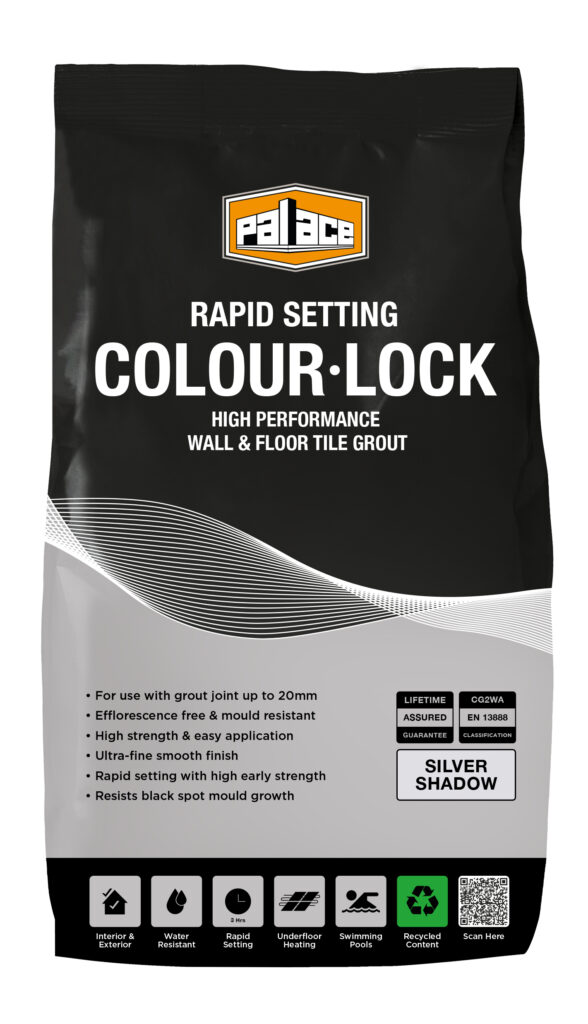
INTRODUCTION It should be noted that due to the variety of application & environmental issues likely to influence the curing of a cement-based grout joint, that it is virtually impossible for the dry composition of the pre pre-blended grout powder to produce localised variations or patchiness in the appearance of the applied grout without first […]
Guide: Tiling On Timber Floors
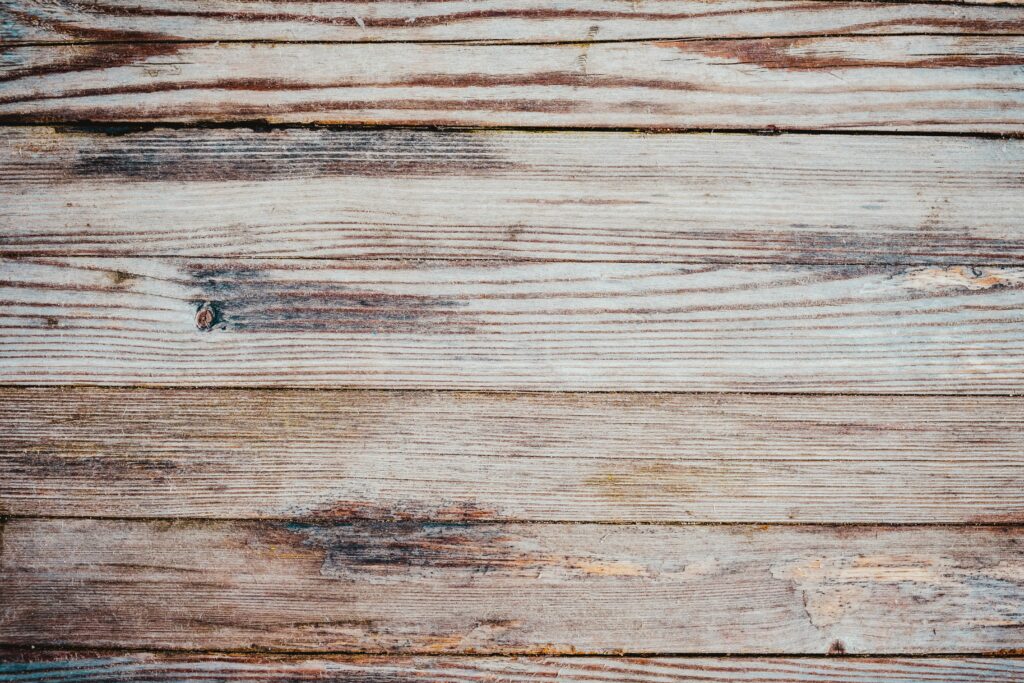
DESIGN CONSIDERATIONS All tile fixing should be carried out in accordance with BS 5385: WALL &FLOOR TILING Part 3 1989 – Code of practice for the design & nstallation of ceramic floor tiles and mosaics and the Tile Association guide – “TILING TO TIMBER SHEETS BOARDS & TIMBER SUBSTRATES. Section 14.4 of BS 5385 part […]
Guide: Waterproofing and Tanking Before Tile Fixing
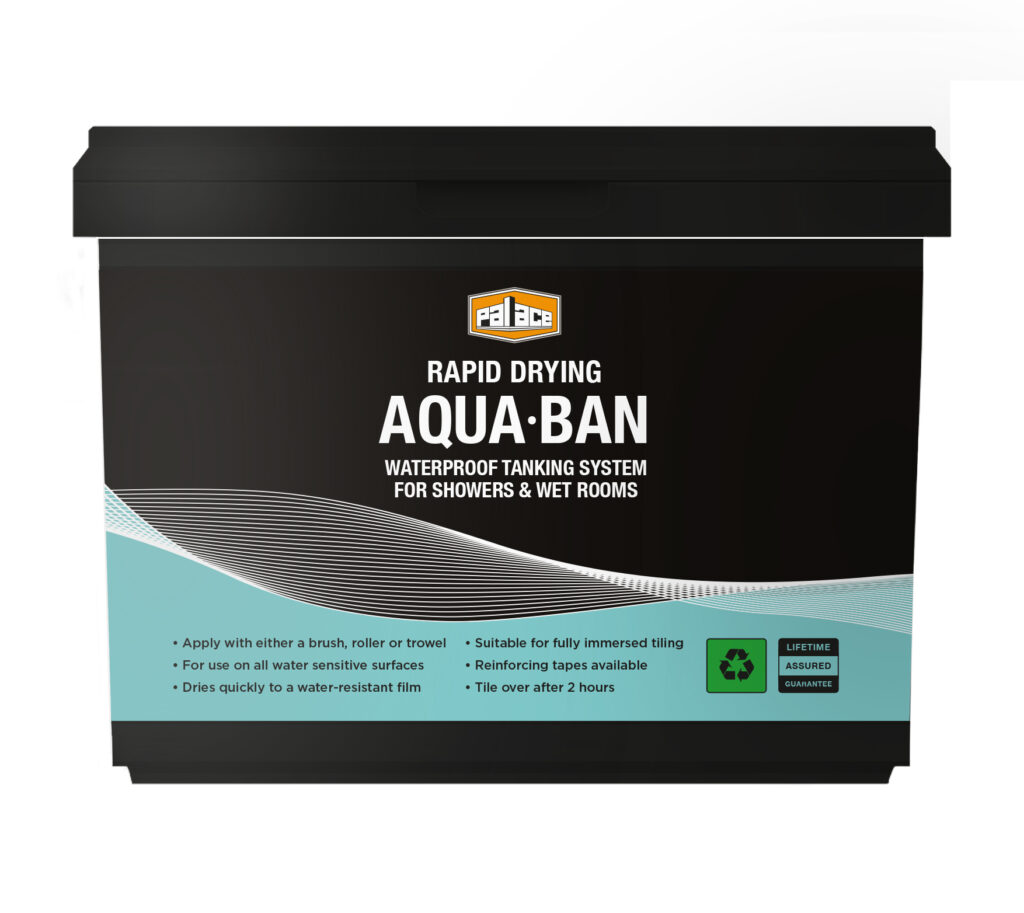
CELLARS & BASEMENTS: Many properties have basements, cellars and vaults that were never designed for modern living. They can suffer from rising damp and penetrating damp and even flooding, and as a result are not used to their full potential. Converting this valuable space into a dry warm living area can greatly enhance property values and […]
Guide: Tiling On Anhydrite Floor Screed
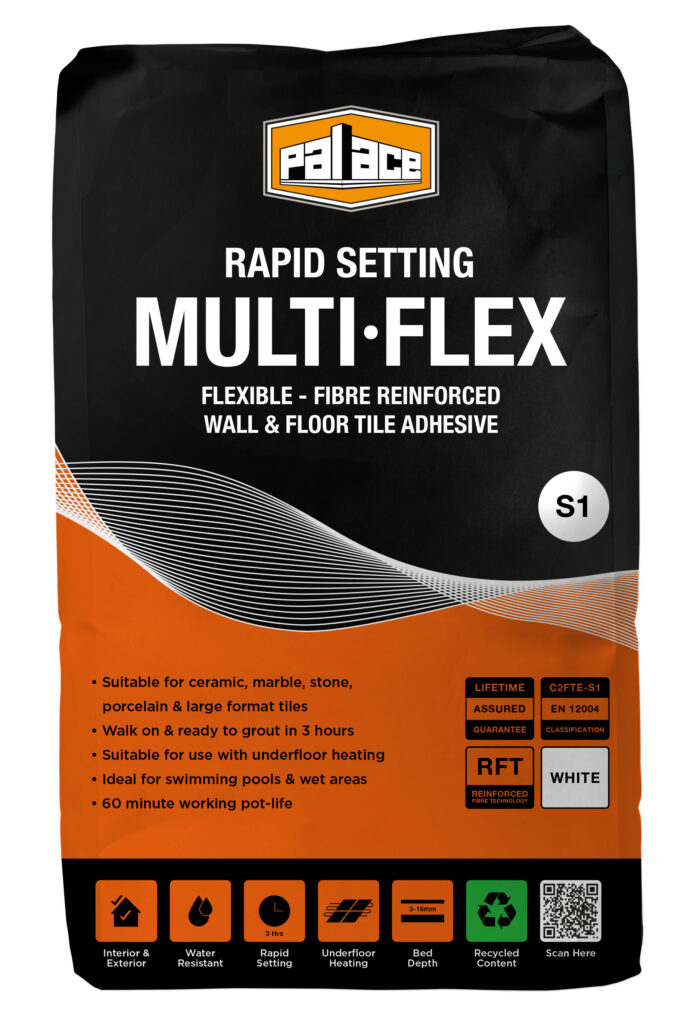
INTRODUCTION Fixing tiles to anhydrite or gypsum-based surfaces requires checks and additional preparation measures to be undertaken to avoid the adverse reaction which can often occur between cement-based adhesive mortars and this type of substrate, which invariably results in lifting and failure of the bond if the following action is not undertaken. DESCRIPTION & IDENTIFICATION […]
Guide: Fixing Large Format Tile & Stone
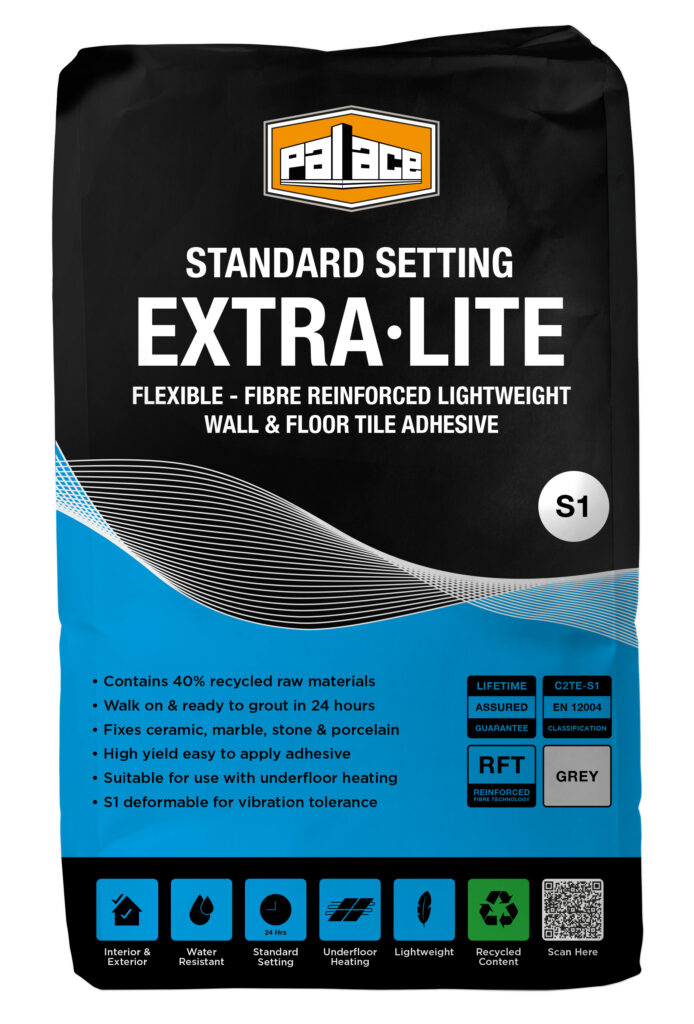
LARGE FORMAT TILE AND STONE NOT ONLY PLACES EXTREME DEMANDS ON THE HANDLING OF THE TILES DUE TO THE OBVIOUS INCREASE IN WEIGHT & DIMENSIONS, BUT ALSO OF GREATER CONCERN IS ENSURING THAT THE TILED FLOOR SURFACE IS SET IN PLACE ON AN EVEN TRUE LEVEL WHILST AT THE SAME TIME ENSURING VIRTUALLY FULL CONTACT […]