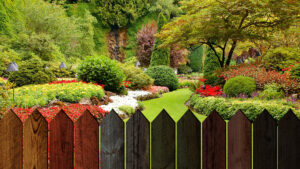
Fenceguard is out of this world!
Fenceguard Is Out of This World! Back in 1982 the only way of treating a fence or shed was to use either Creosote, or a
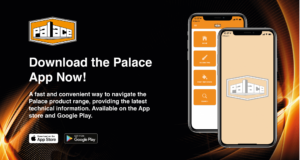
A Smart App for your Smart Phone
A Smart App for Your Smart Phone We are constantly striving to provide our customers with the latest product information, all in one place. This
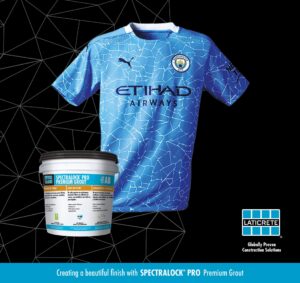
Mark Kennedy – Manchester City 20/21 Home Kit
Mark Kennedy – The Inspiration Behind The 20/21 City Home Kit As the 2020/21 Premier League season gets underway, Palace Chemicals Ltd (which operates Laticrete
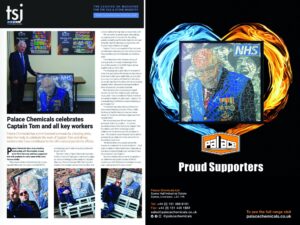
Celebrating Sir Captain Tom’s Great Achievement
Sir Captain Tom’s Great Achievement Palace Chemicals has commissioned a mosaic by a leading artist, Mark Kennedy, to celebrate the work of Captain Tom and
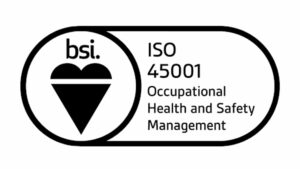
ISO 45001 & Risk Management during Covid-19
ISO 45001 – Risk Management During Covid-19 ISO 45001 our new H&S accreditation & how it helped with risk management during COVID-19 As is the case
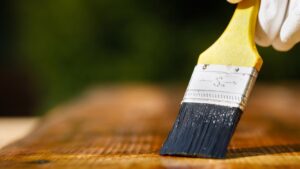
Home & Hardware During Lockdown
Home & Hardware During Lockdown How the lockdown switched demand to “Home & Hardware” and how we reacted as a business In late March earlier
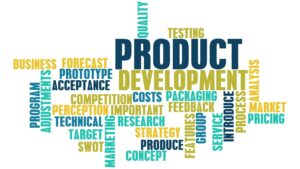
New Products
New Products Listening to the customer and anticipating market demands Palace Chemicals, like most other manufacturing businesses, sends out a lot of marketing information and
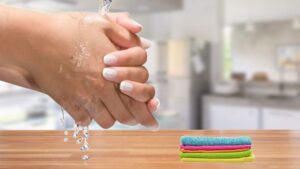
Covid-19 Risks & Opportunities
Covid-19 – Risks & Opportunities How the Risks became an Opportunity for Palace Chemicals introducing Hand & Surface Sanitiser Understanding the risks & opportunities which
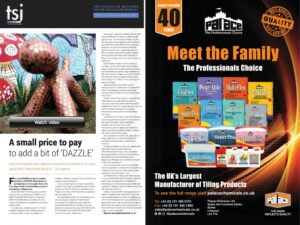
Laticrete Dazzle’s with Spectralock Pro
Laticrete Dazzle’s with Spectralock Pro From grand building projects to quirky artworks: Laticrete UK products are proving time and time again that no job is too big or
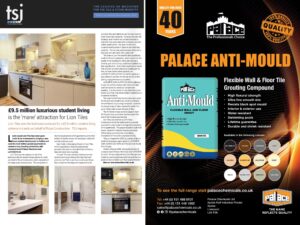
Lion Tiles Roars into action with Student Development
Lion Tiles Roars Into Action with Student Development Leeds-based Lion Tiles has taken great ‘pride’ in its involvement in bringing a new luxury student development to fruition and used the
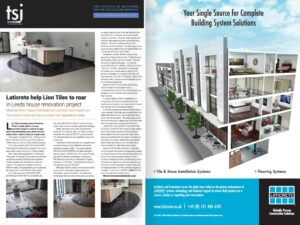
Lion Tiles’ Leeds Renovation
Lion Tiles’ Leeds Renovation Lion Tiles (a trading name of National Tiles) in Leeds took on a house renovation project to extend an open plan
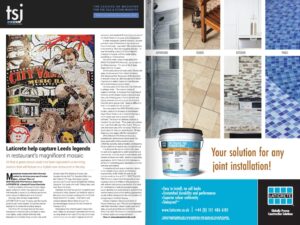
Mark Kennedy’s Leeds Legends Inspired by Laticrete
Mark Kennedy’s Leeds Legends Inspired by Laticrete Manchester-based artist Mark Kennedy crafted the intricate place out of broken glass, Johnson Tiles and Spectralock Pro Premium